How to Address Challenges in the Automotive Parts Industry
The automotive parts industry follows a strong supply chain model. Automotive parts companies must ensure meeting customer demands, including OEM customers and parts customers, under framework agreements with JIT delivery requirements.
The Main Challenges Include:
- Line downtime compensation risk: Parts manufacturers must meet OEM manufacturers' delivery requirements in a JIT manner. If the OEM customer experiences downtime due to delays by the parts supplier, the parts company will bear significant financial risk. Some OEM customers require compensation of 5000 RMB per minute of downtime from the parts supplier. If the OEM experiences a full day of downtime, the parts manufacturer could face over 7 million RMB in economic compensation.
- VMI supply model and offline settlement model: Most OEM manufacturers adopt the VMI supply model and offline settlement model, where parts suppliers manage the finished product inventory at the client's site, and customers pay based on actual parts consumption. With the current market demand uncertainty and the trend of multiple varieties and small batches of parts, ineffective inventory management could result in excessive idle inventory or high inventory levels, affecting company capital utilization efficiency and cash flow.
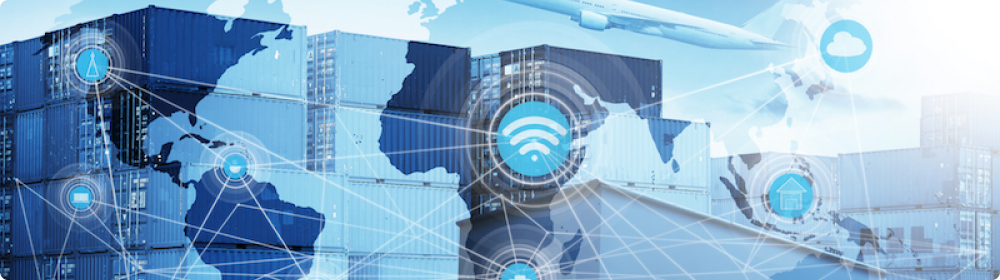
Cost-effectiveness competition: The automotive industry increasingly emphasizes cost-effectiveness competition, thus imposing higher cost control requirements on parts suppliers by OEM customers. Most suppliers face at least one price reduction demand per year, with some OEM customers requiring twice a year. With rising production factor costs, parts suppliers need to adopt leaner and more efficient operational methods to continuously reduce manufacturing cost.
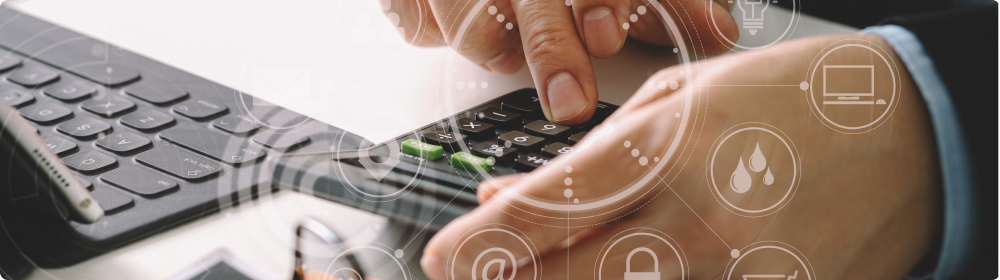
Quality management standards: In the automotive industry, customer quality is evaluated by PPM (parts per million), posing extremely stringent requirements for product quality consistency. Additionally, the automotive industry has legal requirements for product recalls of defective cars, and the losses incurred due to recalls may be borne by the defective parts suppliers. Therefore, precise parts traceability and zero-defect requirements impose very high quality management standards on parts suppliers.
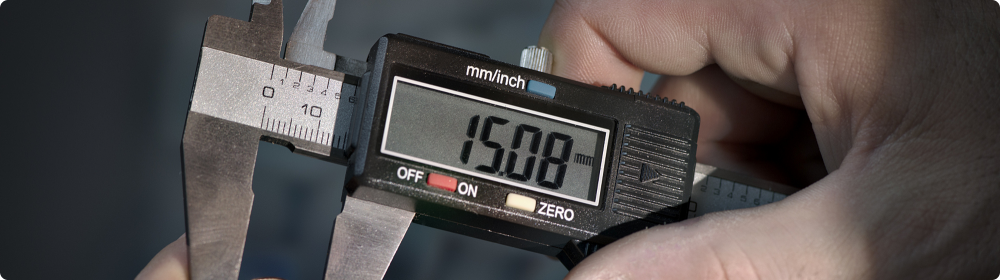
Customized Solutions for the Automotive Parts Industry




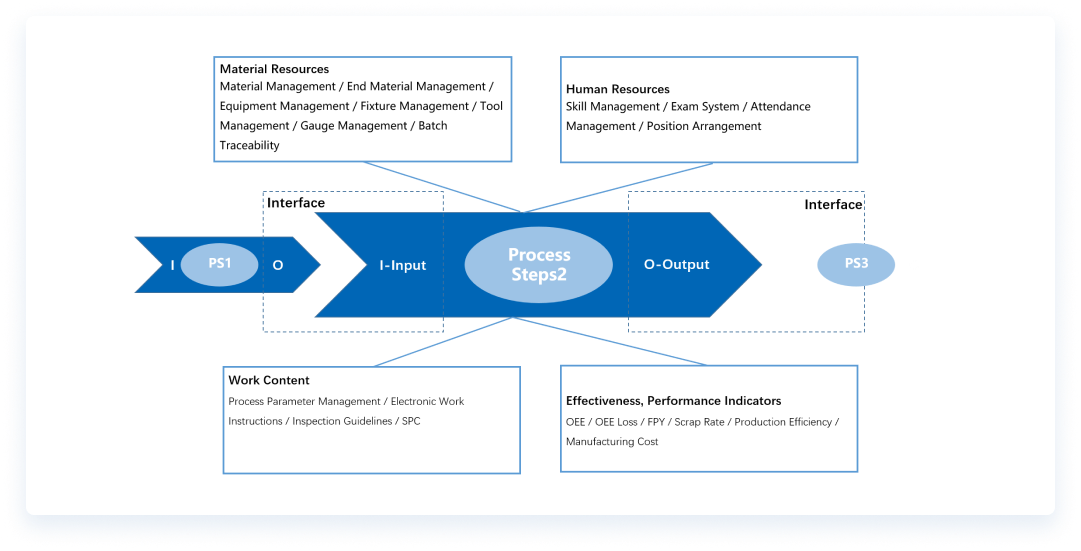
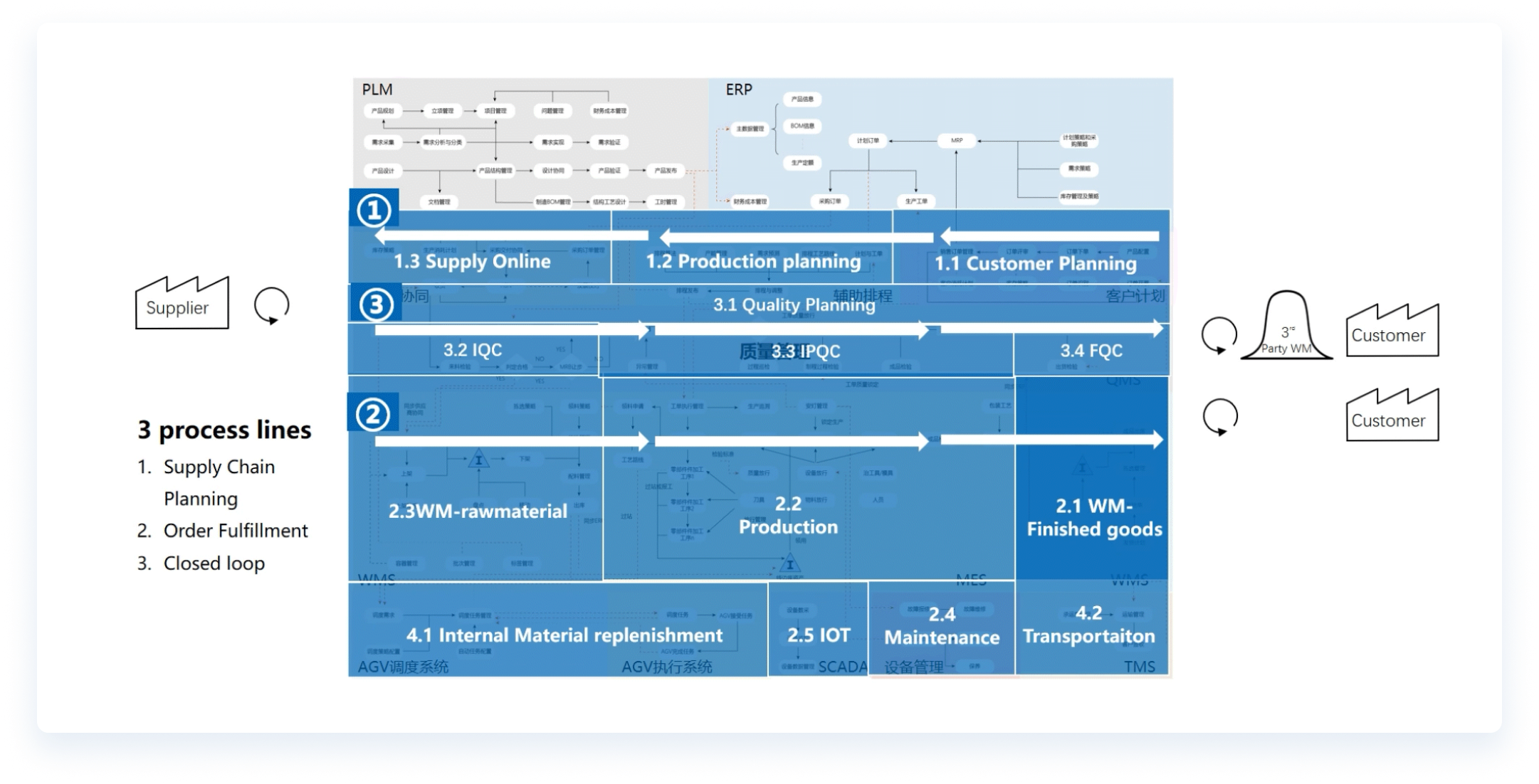
Advantages of LinkedData automotive parts industry solutions
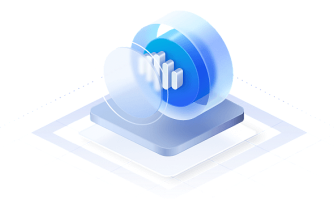
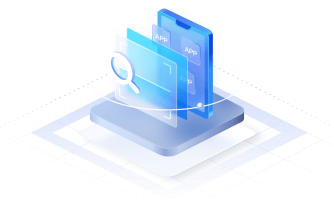
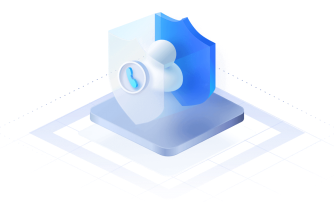